6 Basic Factors Affecting the Size of CNC Machined Parts
Regarding precision engineering, CNC-machined parts are at the forefront of innovation. These components are critical in industries ranging from aerospace to medical devices, where exact specifications make all the difference. Nevertheless, there are challenges in achieving precise dimensions in CNC machining. This article delves into the essential factors that influence the size of CNC machined parts, ensuring you understand how to maintain quality and functionality in production.
Understanding CNC Machined Parts and Their Importance
CNC (Computer Numerical Control) machining transforms raw materials into meticulously crafted parts using automated, computer-controlled tools. CNC machined parts are renowned for their accuracy, durability, and adaptability to complex geometries. However, slight deviations in size or shape can lead to costly errors in assembly or function, making it crucial to understand the factors affecting their dimensions.
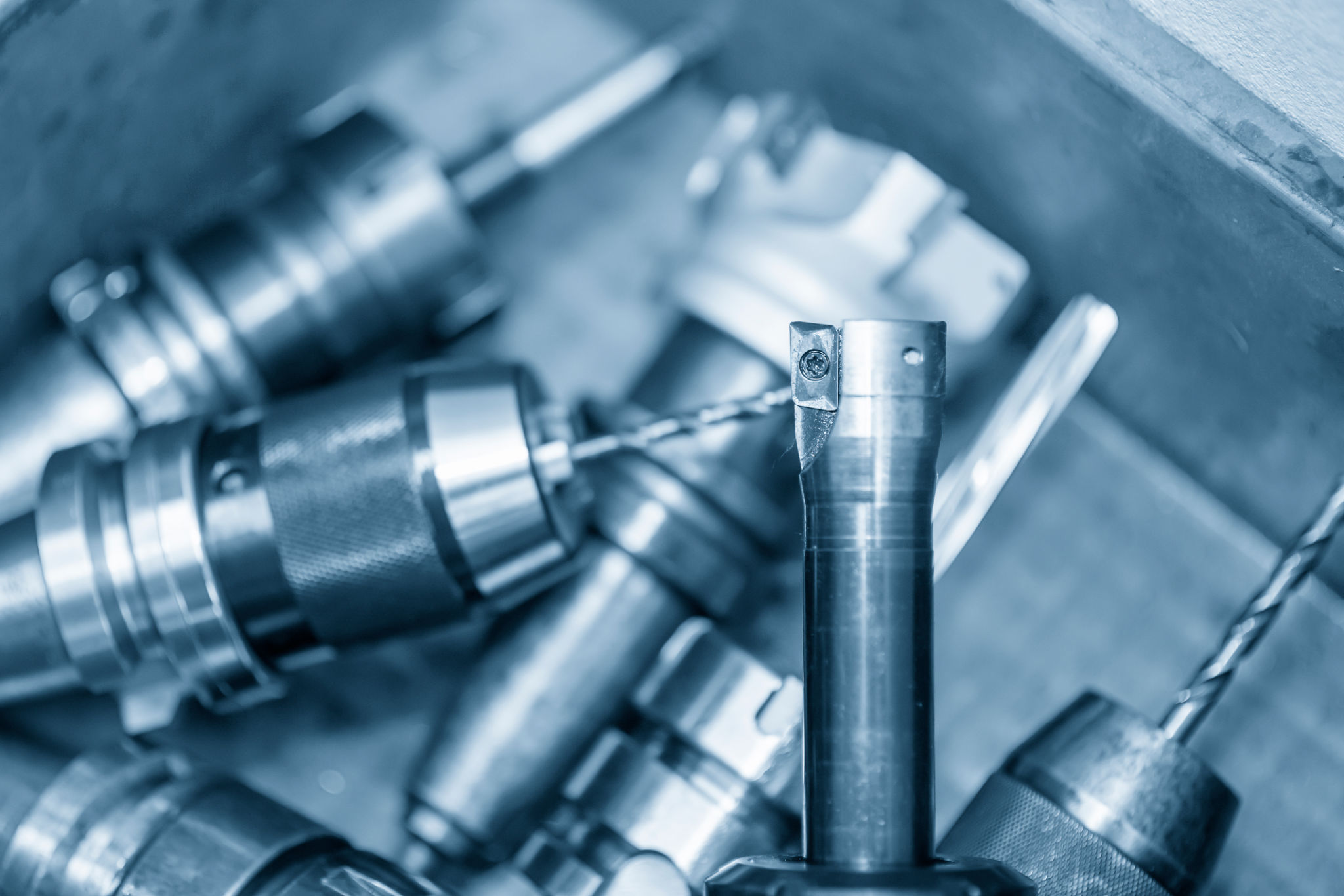
Key Factors That Influence the Size of CNC Machined Parts
1. Material Properties
The choice of material significantly impacts the size and accuracy of CNC machined parts. Different materials—metals, plastics, or composites—have varying properties such as thermal expansion, hardness, and elasticity, influencing machining outcomes. For example:
-Thermal expansion: Metals like aluminum expand more under heat, potentially altering dimensions during machining.
-Hardness: Harder materials like stainless steel may resist cutting tools, leading to potential size deviations.
-Elasticity: Plastics and softer metals can deform under cutting pressure, affecting the final size.
Manufacturers can minimize these variations by selecting the right material and accounting for its properties during design.
2. Tooling Precision and Wear
CNC machining relies heavily on high-precision tools. Over time, cutting tools may wear out or lose sharpness, resulting in:
u Inconsistent cutting depths.
u Increased surface roughness.
u Marginal deviations in the size of the machined parts.
Regular inspection and replacement of cutting tools are essential to maintain consistent part dimensions. Additionally, using specialized coatings on tools can enhance durability and reduce wear.
3. Machine Calibration and Stability
The status of the CNC machine itself is a vital factor. Poorly calibrated or unstable machines can lead to size discrepancies in CNC machined parts. Key aspects to consider include:
l Axis alignment: Misalignment of axes can distort part geometry.
l Backlash: Excessive play in mechanical components can result in inaccuracies.
l Vibration and rigidity: Machines must be mounted on stable surfaces to avoid dimensional errors caused by vibrations.
Routine maintenance and calibration of CNC machines ensure precise operation and consistency across production runs.
4. Cutting Parameters
Optimizing cutting parameters like speed, feed rate, and depth of cut plays a crucial role in controlling part size.
-High speeds may generate heat, causing thermal expansion in both the part and the tool.
-Incorrect feed rates can lead to undercutting or overcutting.
-The depth of cut must align with the material's capabilities to avoid deformation or inaccuracies.
By striking the right balance, operators can maintain the integrity of the CNC machined parts.
5. Environmental Conditions
External elements such as temperature and humidity also have an impact on machining accuracy. For instance:
- Temperature fluctuations may lead to the expansion or contraction of materials, which influences measurements.
- Humidity may lead to corrosion or surface irregularities, especially in metals.
A controlled machining environment mitigates these risks, ensuring stable and consistent outcomes.
6. Human Expertise and Software Accuracy
Even with advanced automation, the expertise of the operator and the quality of the CAD/CAM software play a significant role.
l Human oversight ensures proper setup, material selection, and troubleshooting.
l Accurate programming through reliable software minimizes errors in toolpaths and design interpretation.
Training and skill development are integral to achieving optimal results in CNC machining.
How to Mitigate Size Variations in CNC Machined Parts
To ensure CNC machined parts meet specifications, consider the following practices:
-Conduct material testing before production to understand its behavior.
-Use high-quality and regularly maintained cutting tools.
-Calibrate CNC machines frequently to align with tolerances.
-Make optimizations to machining parameters following the material and part geometry.
-Monitor environmental conditions in the workshop.
-Employ skilled operators and use reliable CAD/CAM software.
Manufacturers can improve precision and reduce rework by putting these strategies into practice.
Conclusion: Ensuring Precision in CNC Machined Parts
CNC-machined parts are indispensable in modern manufacturing, but achieving precision requires careful consideration of numerous factors. From material properties to environmental conditions, each aspect contributes to the overall size and quality of the final product. By understanding and addressing these variables, manufacturers can consistently produce components that meet rigorous standards.
For businesses seeking reliable CNC machining services, SHD PROTOTYPE offers unparalleled expertise in crafting precise, high-quality parts. Whether you need prototypes or large-scale production, we provide outstanding results customized to your specific requirements. Get in touch with us today to discover how our CNC capabilities can turn your designs into reality.