Full Analysis of CNC Milling Machine: Characteristics, Applications and Processing Advantages
Milling Machine Overview
As an important tool for modern processing, CNC milling machines are the basis of machining centers and flexible processing units. Since milling processes are the most complex and involve the most problems, milling processing has always been the focus in the research and development of CNC systems and automatic programming languages.
CNC milling machine processing
The processing surface of a milling machine is usually composed of straight lines, arcs, or other curves. The operator of a traditional CNC milling machine manually adjusts the relative position between the tool and the workpiece according to the requirements of the drawing and performs cutting processing in combination with the speed of the milling cutter to form the required workpiece shape. CNC machine tool processing, on the other hand, subdivides the motion coordinates of the tool and the workpiece into the smallest unit, and the CNC system controls the movement of each coordinate according to the program to achieve precise relative movement between the tool and the workpiece to complete the part processing.
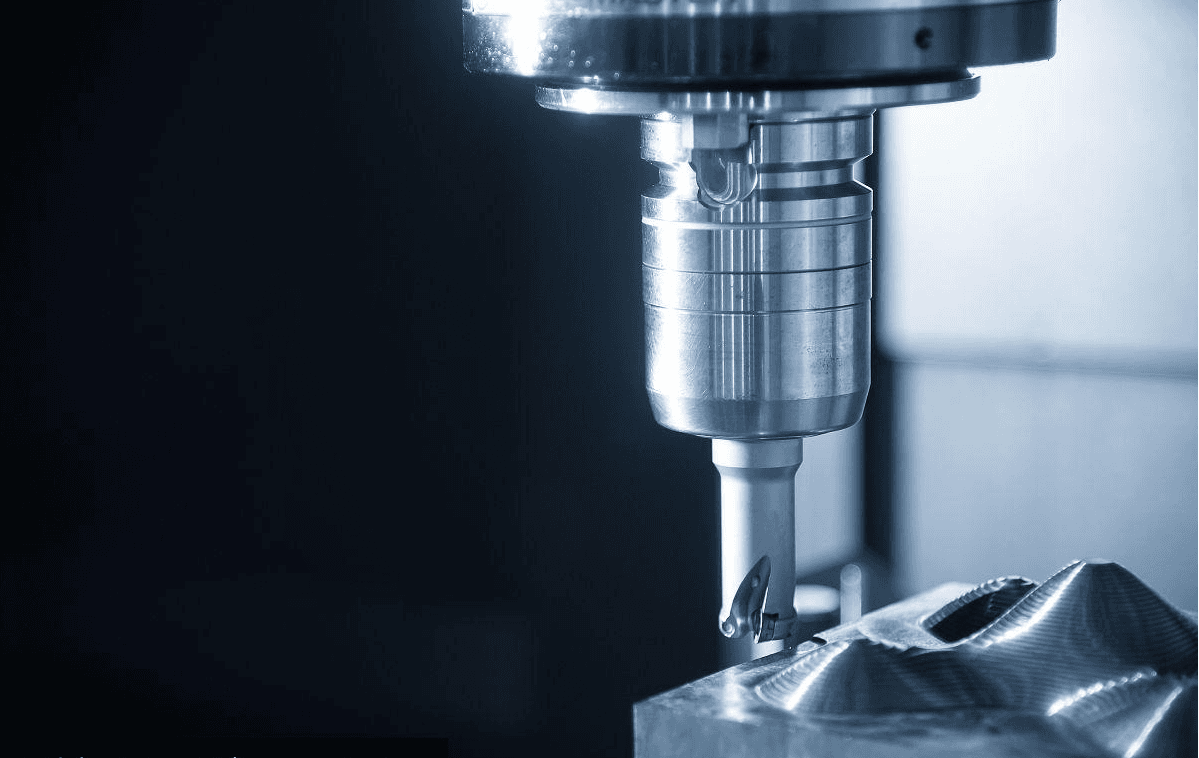
Characteristics of CNC milling
In addition to the basic characteristics of ordinary milling machines, CNC milling also has the following advantages:
1. Strong adaptability and high flexibility: CNC milling machines can process parts with complex shapes or difficult-to-control dimensions, such as molds and shell parts.
2. Precision machining: CNC milling machines have high precision, usually with a pulse equivalent of 0.001mm, and high-precision systems can even reach 0.1μm, ensuring high machining accuracy and stable and reliable quality.
3. High degree of automation: The improvement of automation not only reduces the labor intensity of operators but also supports the automation of production management and shortens the production cycle.
4. Diverse functions: CNC milling machines integrate the functions of milling machines, boring machines, and drilling machines, making the process highly concentrated and significantly improving production efficiency.
5. Fast switching and reuse: When replacing workpieces, CNC milling machines only need to call the machining programs and tool data stored in the system, which greatly improves production efficiency.

Machining considerations
For the machining of frame-shaped planes or unequal height steps, the point-to-line CNC system can meet the requirements. If complex curved surfaces need to be machined, a two-coordinate linkage or three-coordinate linkage system should be selected. Adding a CNC dividing head or a rotary table to an ordinary CNC milling machine can upgrade the system to a four-coordinate system to machine complex parts such as spiral grooves and blades.
Size and precision
Small-sized lifting table CNC milling machines, with a worktable width of generally less than 400mm, are suitable for the processing of small and medium-sized parts and complex surface milling. Large-sized gantry milling machines, with a worktable width of more than 500-600mm, are suitable for the processing needs of large-sized complex parts. The precision of CNC milling machines is generally higher than the national standard. The positioning accuracy of linear motion coordinates is 0.04/300mm, and the repeat positioning accuracy is 0.025mm, which can meet the processing needs of most parts. For high-precision parts, precision CNC milling machines can be selected.
Batch production
For mass production, special milling machines are ideal. If it is small and medium batches and periodic repetitive production, CNC milling machines are very suitable. The fixtures and programs prepared in the first batch of production can be reused. In the long run, it is an inevitable trend for highly automated milling machines to gradually replace ordinary milling machines.
Main functions of CNC milling machines
1. Point control: mainly used for hole processing, such as positioning drilling, reaming, reaming, etc.
2. Continuous control: milling planes and curved surfaces through a straight line, arc, or complex curve interpolation.
3. Tool radius compensation: automatically calculate the tool center trajectory to ensure that the contour of the machined workpiece meets the design requirements, and can compensate for tool wear and machining errors to achieve rough machining and finishing.
4. Tool length compensation: compensate for the length deviation of the tool after tool change, and control the axial positioning accuracy of the tool.
5. Fixed cycle machining: simplify programming workload, suitable for repetitive operations.
6. Subroutine function: write the same or similar machining parts into subroutines, which are called by the main program to optimize the machining process.

Machining range of CNC milling machines
1. Plane machining: CNC milling machines can mill horizontal planes, front planes, and side planes, which can be completed using a two-axis and a half-controlled CNC milling machine.
2. Surface machining: For complex surfaces, a three-axis or multi-axis linkage CNC milling machine is required.
Equipment and tools
1. Fixtures: Commonly used fixtures include flat-nose pliers, magnetic suction cups, and pressure plate devices. For medium and large batches or workpieces with complex shapes, a combination fixture can be designed, and pneumatic or hydraulic fixtures can be used through program control to achieve automatic clamping and improve work efficiency.
2. Tools: The milling tools commonly used by machinists are as follows: end mills, end mills, profile mills, and hole processing tools.