The Expertise Behind Precision CNC Machining Services
Precision CNC machining is a critical technology in modern manufacturing, enabling the creation of highly accurate and complex parts with exceptional dimensional tolerance. This process utilizes computer numerical control (CNC) machines to produce components that meet strict quality standards, making it essential in industries where precision is paramount. From aerospace and automotive to medical devices, precision CNC machining plays a vital role in ensuring that parts meet the exact specifications required for safety, performance, and reliability.
What is Precision CNC Machining?
Precision CNC machining involves the use of advanced CNC machines to perform intricate machining operations with a high degree of accuracy. The process begins with a detailed CAD (Computer-Aided Design) model of the part, which is then converted into a CAM (Computer-Aided Manufacturing) program. This program controls the CNC machine, guiding its movements along multiple axes to precisely shape the workpiece. The result is a component that closely matches the design specifications, often with tolerances as tight as ±0.001 inches or less.
Features of Precision CNC Machining:
- High-Dimensional Accuracy: Precision CNC machining is known for its ability to produce parts with extremely tight tolerances, ensuring that components fit together perfectly in assemblies and function as intended.
- Complex Geometry: CNC machines can handle complex geometries that would be difficult or impossible to achieve with traditional machining methods. This capability is especially important in industries where intricate designs are common, such as aerospace and medical devices.
- Consistency and Repeatability: Precision CNC machining allows for consistent production of parts with minimal variation, even in large batches. This repeatability is crucial for maintaining quality control in manufacturing processes.
- Surface Finish Quality: The precision and control offered by CNC machines result in superior surface finishes, reducing the need for additional post-processing steps such as polishing or grinding.
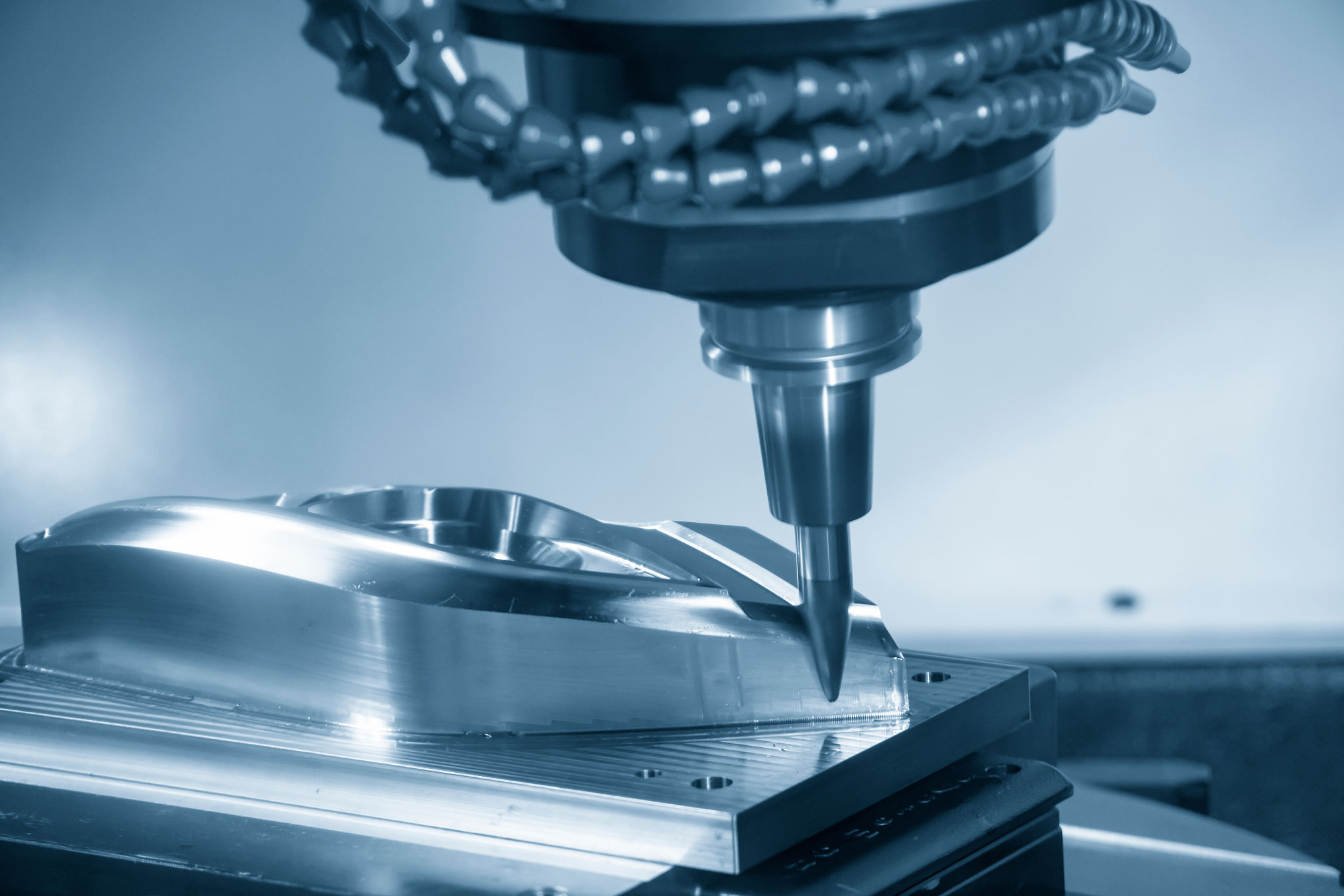
Applications of Precision CNC Machining:
Precision CNC machining is widely used across various industries due to its versatility and accuracy:
- Aerospace: In the aerospace industry, components must meet stringent standards for safety and performance. Precision CNC machining is used to produce parts such as turbine blades, engine components, and structural elements with tight tolerances and high surface quality.
- Automotive: Automotive manufacturers rely on precision CNC machining to create engine parts, transmission components, and other critical elements that require exacting tolerances for optimal performance.
- Medical Devices: The medical industry demands precision in the production of implants, surgical instruments, and diagnostic equipment. CNC machining ensures that these components meet the necessary specifications for safety and effectiveness.
- Electronics: Precision CNC machining is also essential in the electronics industry, where it is used to produce connectors, housings, and other components that require high levels of accuracy.
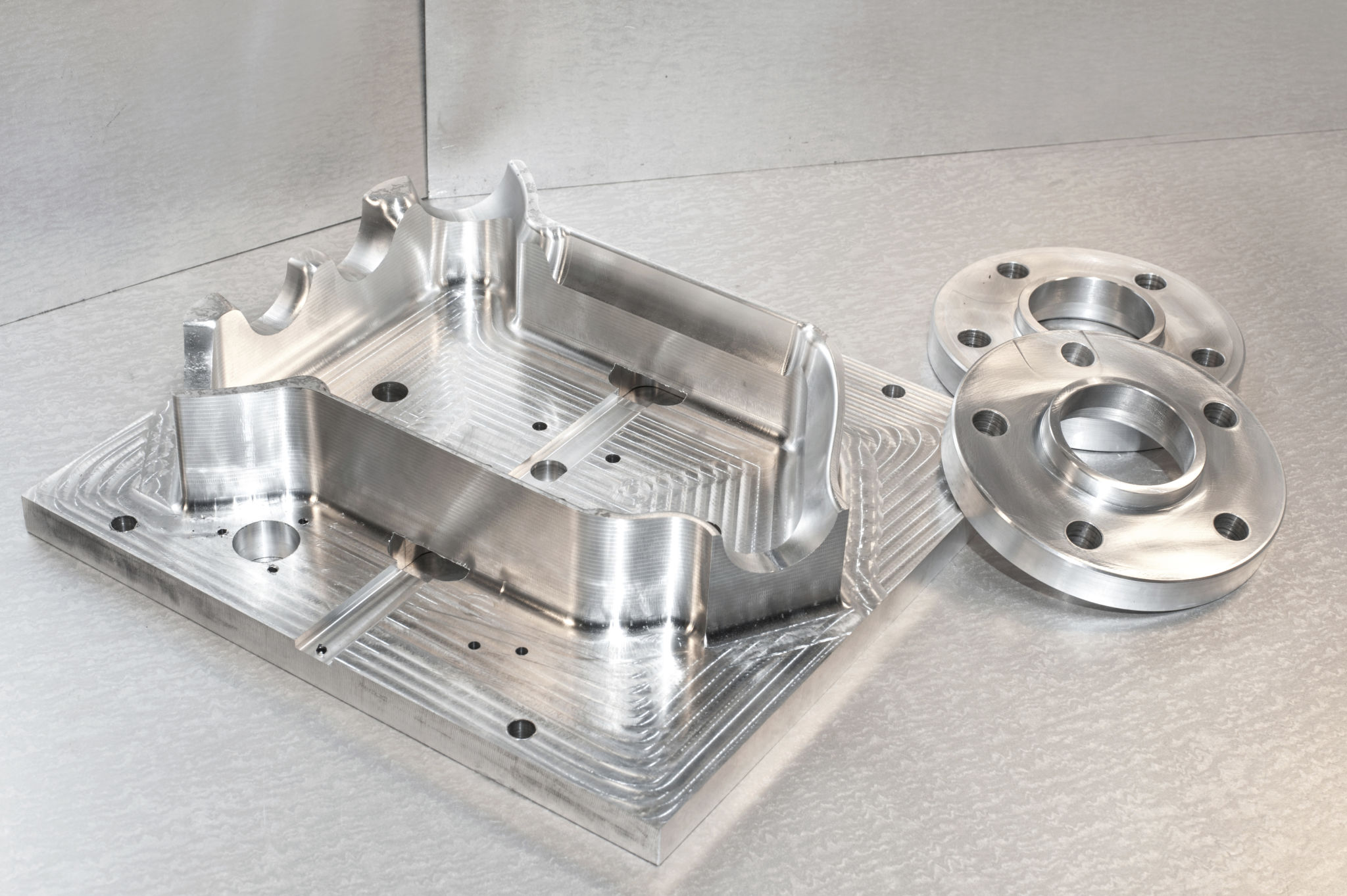
Precision CNC Machining Process:
The precision CNC machining process involves several key steps, each of which contributes to the overall accuracy and quality of the final product:
1. Design and Programming:
- The process begins with the creation of a detailed CAD model of the part. This model is then translated into a CAM program, which defines the tool paths, cutting parameters, and other machining instructions.
- Engineers must carefully plan the machining process, taking into account factors such as material properties, tool selection, and machining sequence to ensure optimal results.
2. Machine Setup:
- The CNC machine is set up with the appropriate tools and fixtures, ensuring that the workpiece is securely held in place during machining.
- Precise calibration of the machine's axes is essential to achieving the required tolerances and surface finishes.
3. Machining:
- During the machining phase, the CNC machine follows the programmed tool paths to remove material from the workpiece, gradually shaping it into the desired form.
- Multiple passes may be required, especially for complex geometries or parts with tight tolerances.
4. Inspection and Quality Control:
- Once machining is complete, the part undergoes thorough inspection using precision measurement tools such as coordinate measuring machines (CMMs) and laser scanners.
- Any deviations from the design specifications are identified and corrected, ensuring that the final product meets the required standards.
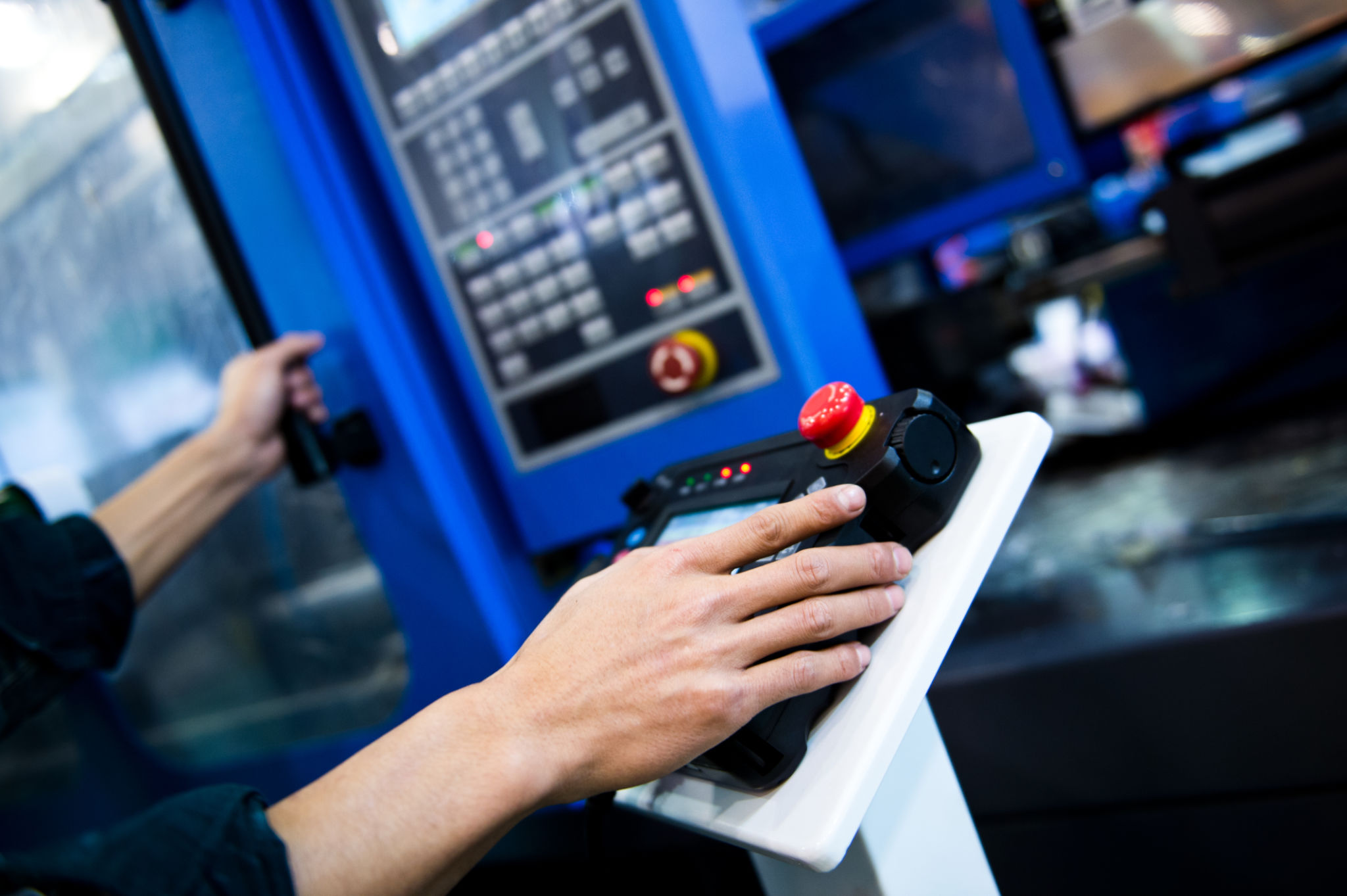
Challenges of precision CNC machining
Although precision CNC machining has many advantages, it also has some difficulties and challenges:
- Material Selection: The choice of material can significantly impact the machining process, as some materials are more difficult to machine than others. Engineers must carefully consider factors such as hardness, machinability, and thermal expansion when selecting materials.
- Tool Wear: The precision of CNC machining is highly dependent on the condition of the cutting tools. As tools wear down, they can cause variations in the dimensions and surface finish of the parts. Regular tool maintenance and replacement are essential to maintaining accuracy.
- Thermal Effects: The heat generated during machining can cause thermal expansion of the workpiece, leading to dimensional inaccuracies. Managing heat through coolant systems and careful process control is crucial to maintaining precision.
Precision CNC machining is an indispensable technology in modern manufacturing, offering unparalleled accuracy, consistency, and versatility. By combining advanced machine tools with meticulous planning and quality control, manufacturers can produce parts that meet the most demanding specifications. Whether in aerospace, automotive, medical, or electronics, precision CNC machining continues to play a vital role in the production of high-quality components that power our world.