Wire Cutting EDM: The Secret Weapon for High-Precision Manufacturing
Wire cutting of electrical discharge machining (abbreviated as "wire cutting") is a technology that uses electrode wire (such as molybdenum wire, tungsten-molybdenum wire, etc.) as a tool electrode and realizes workpiece processing through spark discharge under the action of a pulse power supply. When the electrode wire contacts the workpiece, the high temperature generated causes the workpiece surface to partially melt or even vaporize, completing the material removal. The wire-cutting machine tool uses the precise movement of the XY pallet and the UV pallet to move the electrode wire along the predetermined trajectory, thereby processing the required workpiece shape.

Concept of Wire Cutting EDM
CNC Wire Cutting EDM (Wire Cutting EDM), like EDM forming, uses electrical energy and thermal energy to process the workpiece. This technology can process conductive materials that are difficult to process with traditional cutting methods, such as metals or semiconductor materials with high hardness, high brittleness, high toughness, and high heat sensitivity. Since it was put into use in the late 1950s, wire cutting has developed rapidly due to its high precision and high automation. It has been widely used in manufacturing industries such as instruments, meters, electronics, and automobiles, and has become one of the key technologies for precision parts and mold manufacturing.
Processing principle
Wire cutting uses the phenomenon of electrical corrosion to convert the spark discharge generated between the electrode wire and the workpiece into thermal energy, thereby locally melting and removing the material. By controlling the movement trajectory of the electrode wire, precision processing of complex-shaped workpieces can be achieved.
Equipment composition
The CNC wire-cutting machine tool is mainly composed of the following parts:
·Workbench: used to install fixtures and workpieces, driven by stepper motors to complete the longitudinal and lateral movement of the workbench.
·Wire feeding mechanism: including wire storage drum, wire feeding motor guide wheel, etc., the electrode wire reciprocates at a set speed to achieve cutting processing.
·Liquid supply system: provides the working fluid required for the cutting process, cools the electrode and workpiece, and removes the waste chips generated during the processing.
·Pulse power supply: generates pulse current for cutting, which is an important factor affecting the processing accuracy.
·Control system: realizes digital control of the processing process and can perform automated operations according to the processing requirements of different workpieces.
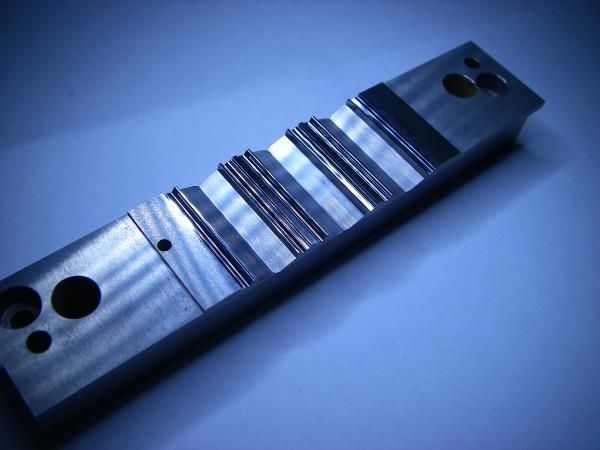
Features and uses
Electro-spark wire cutting has the characteristics of high precision and high flexibility. It can process workpieces with complex shapes and special materials and is particularly suitable for mold manufacturing. Its main features include:
1. Non-contact processing: the electrode wire does not directly contact the workpiece, reducing the deformation of the workpiece.
2. Save electrode cost: use the electrode wire as a tool electrode, without the need for a special electrode.
3. Strong processing flexibility: The CNC system can realize the automated processing of workpieces of different shapes through programming, which is suitable for the production of small batches and complex parts.
4. Multi-axis linkage: It can process complex parts such as tapers, and upper and lower shaped bodies.
5. Wide adaptability: It can process high-hardness or brittle materials, and has low requirements for tool hardness.
Safety operation specifications
When operating CNC wire-cutting machine tools, the operator must be familiar with the performance and structure of the machine tools and strictly abide by the operating procedures. Here are the safety considerations to keep in mind when machining:
· Pre-start inspection: Ensure that all parts of the machine tool are intact and well-lubricated, and the circuit connection is normal.
· Workpiece installation: The workpiece must be firmly clamped to ensure that it does not collide with the wire rack during processing.
· Start sequence: Correctly start the various functions of the machine tool to ensure a normal supply of working fluid and stable movement of the electrode wire.
Although CNC wire-cutting processing has a wide range of application prospects, its operation is complicated and requires the operator to have a high level of technical skills and safety awareness. Strictly following the operating specifications can not only ensure processing accuracy but also effectively avoid equipment damage and personal safety accidents.